Introduction
The soft hand feels of shirts and woollen garments, the smooth fabrics of our upholstery, and the seamless finish of paints and primers – are the quiet magic of levelling agents at work. In the dynamic landscape of textile processing, levelling agents play a pivotal role in ensuring consistent dye penetration and uniform colouration, which are key to maintaining quality standards across batches.
But like everything else, even these chemical workhorses are evolving. With industries leaning into sustainability and smarter formulations, levelling agents are getting a serious glow-up. From their behind-the-scenes brilliance in dyeing processes to the latest eco-friendly tweaks catching global attention, a lot is bubbling under the surface. Read on to peek into the world of levelling agents, where science meets style and performance pairs with planet-first thinking.
Levelling Agents: Roles, Mechanisms & Key Industry Segments
These agents may be minor players in the formulation, but they have a wide-reaching impact across several industries, each with its unique demands for precision, durability, and aesthetics.
Depending on the dye class, reactive, acid, dispersed or direct are the different types of levelling agents used, ranging from non-ionic to anionic and cationic surfactants. Mechanistically, levelling agents work by forming temporary complexes with dye molecules or altering fibre-dye interactions, slowing the exhaustion rate.
In the textile and apparel industry, levelling agents ensure flawless appearance and uniform colour build-up, whether in high-street fashion or luxury couture. The home textile sector, which includes curtains, upholstery, bed linens, and carpets, relies heavily on levelling agents to maintain colour consistency across large fabric surfaces.
Materials like seat fabrics, floor mats, headliners, and door panels, also known as automotive textiles, get their longevity, heavy-duty performance and protection against sunlight, friction and fading from these chemical additives.
Levelling agents support high-performance dyeing in technical textiles and industrial fabrics like filtration media, geotextiles, safety gear, and performance apparel. The versatility of levelling agents also extends to leather processing and paper dyeing, ensuring smooth, uniform colour application on non-textile substrates.
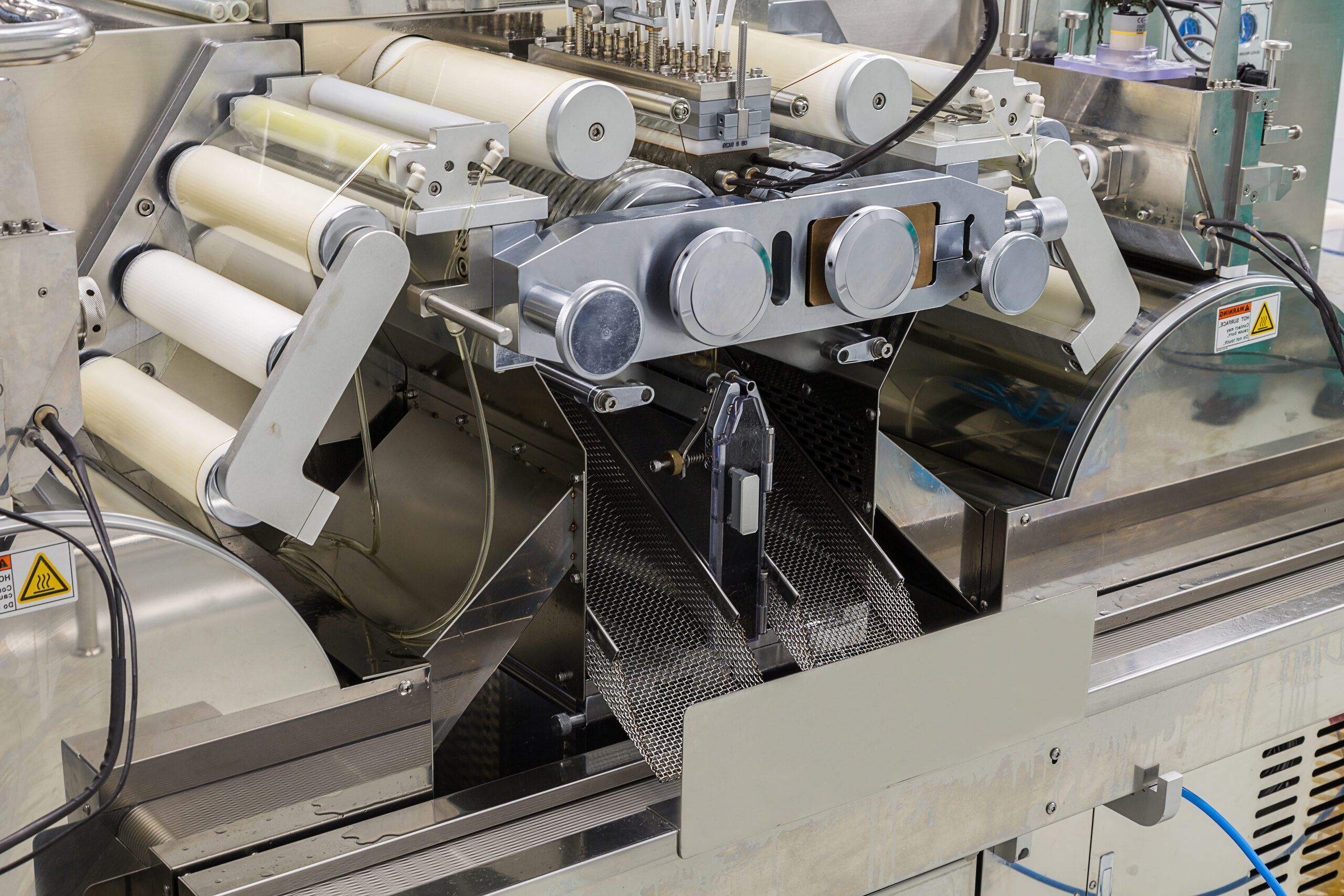
Market Movements: Current Demand, Key Players & Growth Forecasts
In India, the market for levelling agents was valued at approximately 2.93 billion USD in 2024 and is projected to reach 3.59 billion USD by 2030, growing at a CAGR of 3.63% during the forecast period. Besides importing a chunk of the annual requirement from Germany, Italy and China, our nation also exports a hefty margin to the neighbouring countries and parts of Southeast Asia.
The demand is particularly high in regions with dense textile clusters like Gujarat, Tamil Nadu, and Maharashtra. Internationally, demand is rising for cleaner, low-foaming, and biodegradable formulations, a trend that’s influencing Indian manufacturers to invest in eco-conscious R&D.
Beyond textiles, the versatile application of levelling agents across industries such as digital printing, paper processing, and upholstery manufacturing is further fuelling market expansion. As these industries continue to scale up, driven by rising consumer demand for high-performance finishes and aesthetic consistency, the levelling agent segment is expected to witness sustained growth, supported by evolving formulations and multi-industry adaptability.
Sustainable Formulations & Future-Ready Alternatives of Levelling Agents
The future of levelling agents lies in sustainability, and the gradual shift can be seen on the horizon. As the global chemical industry moves toward greener practices, scientific researchers are engineering next-gen levelling agents that offer high performance with low ecological footprints. These future-ready formulations are being developed with a focus on biodegradability, low toxicity, and reduced water and energy consumption during processing. Innovations include enzymatic levelling agents, which function efficiently at lower temperatures and pH levels, and smart polymers that adjust their activity based on the fabric and dye used.
Bio-based alternatives derived from plant oils, amino acids, and naturally occurring surfactants like saponins and lecithin are gaining momentum. These organic agents are safer for wastewater systems and align with the textile industry’s rising commitment to circularity and clean manufacturing. As regulatory pressures and eco-conscious consumerism grow, these sustainable alternatives are poised to become the new norm, transforming levelling agents from chemical necessities to environmental allies.
FAQs
- What are levelling agents, and why are they used in textile processing?
- Levelling agents are speciality chemicals used primarily in dyeing processes to ensure uniform distribution of dyes across fabric surfaces. They slow down the dye uptake during initial phases, allowing for even penetration and preventing patchiness or streaks.
- How do levelling agents differ across various dye types?
- Levelling agents are formulated to work with specific dye classes — such as reactive, dispersed, or acid dyes. For instance, non-ionic or anionic levelling agents are often preferred for reactive dyes, while cationic agents work better with acid dyes used for wool and nylon.
- What market trends are influencing the demand for levelling agents today?
- Key trends include a shift toward low-temperature, high-performance formulations, growing demand from emerging textile hubs in Asia-Pacific, and increasing adoption of sustainable, biodegradable variants. Environmental regulations and global certifications are also pushing the industry toward cleaner alternatives.
- Are eco-friendly levelling agents as effective as traditional ones?
- Yes. Modern eco-friendly levelling agents have been engineered to offer comparable, and often superior, performance without compromising environmental safety. These newer formulations are free from APEOs, formaldehyde, and other harmful substances, making them suitable for GOTS- and ZDHC-compliant facilities.
- What should manufacturers look for when choosing a levelling agent?
- Factors include fabric type, dye class, application temperature, compatibility with other auxiliaries, and compliance with environmental standards. Additionally, sourcing from a reputed chemical manufacturer ensures product consistency, technical support, and access to innovation-driven solutions.
Sources: